Project Title
SWITCH
Overview
Thesis project to connect the flexibility of design that digital typefaces allow to the rigidity of letterpress printing.
My Role
Research, Design, and Production
Planning
Before designing anything I needed to clarify what my goals were, what steps I'd need to take, and what the finished product would look like.
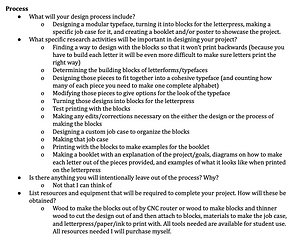

After going through this process, I could essentially narrow down my project to the following statement:
I want to bring the flexibility of designing digitally to the letterpress by creating an easy to use modular woodblock typeface.
Research
I needed to look into existing modular typeface systems, how letterpress type is made, and ways I could create my own set.
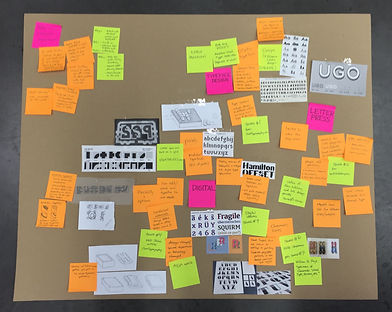
This board kept everything organized as I found more resources and had more ideas.
My research turned up that there were a few main ways to create modular typefaces: simple grid, complex grid, letterform anatomy, and chromatic/layered. It also provided me with resources on how to design a typeface, what is needed to make successful letterpress type, and how to print on a letterpress for the best results.
Typeface Design
The first thing to do was create the typeface. I explored a few different directions to determine which modular style I wanted to go with.


I knew I wanted to make additional styles for my typeface, so I chose to go with the letterform anatomy option. After a lot of trial and error, I narrowed down the number of unique pieces needed to 23 printing and 3 spacing.
I knew I wanted to make additional styles for my typeface, so I chose to go with the letterform anatomy option. After a lot of trial and error, I narrowed down the number of unique pieces needed to 23 printing and 3 spacing.
Piece Design/Construction
My next hurdle was figuring out how to produce the pieces. There were a lot of things to keep in mind including:
-
What materials should I use
-
How to keep each piece level and square so they could line up and print together
-
How the user will compose with them
-
How I can reduce user error for misprints
-
If composed off the press, how to transfer pieces to the press
After careful consideration I came to the following conclusions:
-
Users will compose with the print side facing down since creating each letter from multiple pieces left too much room for error
-
What each block will print then needs to be shown on the back
-
Similar looking pieces need to be differentiable
-
Because the design will be upside down, there must be a way to efficiently flip everything over
-
The best way to do this would be to attach the pieces to something securely enough to flip but not so securely that it becomes difficult to remove them
Combining all of those ideas together ultimately led me to this construction for each piece.

The top piece of wood would have the design laser engraved into it.
Magnets would be used to flip pieces over/transfer them to the press. This would require an additional piece of wood to hold the magnet in place. Another piece of wood would be attached over the magnet to create a smooth back.
Finally, on the back there would be an image of what the block prints.
Job Case
The last thing I needed to complete this project was to create a job case to keep all the pieces together. Since this wasn't a traditional woodblock typeface, a traditional job case wasn't going to cut it.
I determined how many of each piece I would need based on how frequently it gets used to create letters and how frequently those letters appear in English (for example, there are two pieces in the typeface that are only used to create the letter T but since that's such a common letter to use I decided to make three of each of them). Using those numbers I then created a layout for the job case.
Final Results
Reflections
Self-directed work can be challenging but I'm really proud of where I ended up with this. I found that as problems came up I really enjoyed working through them and I learned so much about my personal work style throughout this process.
There are of course things I would change. I'm not as convinced now as I was at the time that magnets were the way to go. I see the value in color coding but maybe fewer colors or more toned down versions would be a better direction. And there's definitely an easier way to create each piece - maybe something with resin or even casting lead type - but with the materials and machines I had access to at the time I'm happy with the project's outcome.